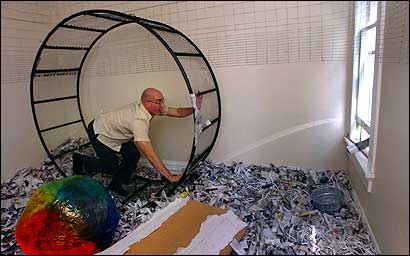
Its on the brain
ALL TOGETHER NOW
Im writing these blog entries in the order that I constructed my cat wheel which means some steps done for aesthetic purposes occurred before some of the more important functional steps. However, that's the way it goes sometimes.
THE COVERING 1
Around the outside of the wheel I wanted to have something that would cover the beams under the track. For this I used 810mm x 1200mm 3mm MDF cut to slightly larger dimensions than the plywood track (417mm x 1200mm). The extra length was due to MDF not having any grain to use in assisting the bend so I used the longer lengths resulting in fewer individual pieces needed. The extra width was so it could cover the beams and extend over the 12mm thick plywood circle. I screwed the MDF into 12mm plywood circle on the back edge of the wheel and into each beam along the front. Again, I took into consideration the longer timber screws that will be going into the beam and left a couple of centimetres from the edge when screwing down the MDF.
Unfortunately the cut pieces didn't make an even fit around the wheel leaving about a 10cm gap between the first and last piece. At the time of writing this post I haven't fixed it yet, but I assume I will just cut a small piece to fill the gap. However, the problem here is how to have them run smooth against each other because, unlike the track, I'm not wanting to overlap any pieces. The other issue this has caused is the MDF boards not joining at a beam, and even if they did I wouldn't want to drill both boards into the one beam. This resulted in the edges of the MDF sticking up. I fixed this by attaching a little latch that could be screwed into each MDF holding them tight enough together to lie flat. Apparently MDF doesn't hold a screw well on its own because there is not wood grain to hold the screw thread, so I bought some screws with back nuts so the MDF wouldn't be holding the screw like the beams and the plywood are holding the other screws. The oddness of this will end up being covered up by the front panels.
THE CASTOR
The Castor/spinning mechanism ended up being a bit tricky, and was the main thing I was referencing in the intro of the previous post. In the end the solution to the problem was very simple. Ill explain later.
The positioning of the castor directly in the middle of the plywood circle was done by using the hole from the nail that was used to draw the original circle outline. I positioned the castor then drilled into the four bolt holes of the castor through the plywood circle. The bolts that came with the castor were longer than I wanted, so if I had used them it would have meant the long screw end of the bolt protruding in the middle of the cat wheel because doing it the other way would have meant the bolt length would have prevented the castor from rotating. So I bought shorter bolts so I could have the nicer presentation of the bolt head in the middle of the wheel while the screw end didn't interfere with the rotation.
Before attaching the castor to the wheel I positioned the castor on the upright of the frame, and drilled it into position about 600mm up the frame. Based off the circle's radius of 582.5mm plus the uprights 45mm height off the floor that the legs provide, a height of 600mm for the castor will give the wheel plenty of clearance off the floor but not too high so the cats wont be able to reach it.
From here it was "simply" attaching the two pieces together and locking it in place.
The issue I mentioned before was that when I first attached the wheel, castor and frame together, as seen in the pic above, the wheel was on a slight angle towards the rear at the bottom and would hit the support beams of the frame as it spun. I wasn't sure why this was happening and initially I thought it was because the castor couldn't sit flush against the upright due to it being rounded on one side creating an angled lean of the wheel. So, rather than think about it any harder, I went down to the shop and bought a couple of different casters to try that would sit flush. This resulted in proving one thing for sure .... I need to think harder. The angle of the wheel became worse and it was now rubbing so hard it couldn't spin smoothly. The plus side was that the new castors illustrated the problem much clearer. The weight of the wheel was causing the rotating part of the castor to bend downwards. My original castor was the most heavy duty and bent the least, so I went back to using the original castor but I added a piece of the 42mm x 19mm timber to the upright in order to give the wheel more clearance between it and the frame.
The Joy Of Drilling, or
Trial and Error: The story of a guy who measured once and cut many many times
Next: the finishing touches, an uninterested cat and the next project: cat adoption.
No comments:
Post a Comment